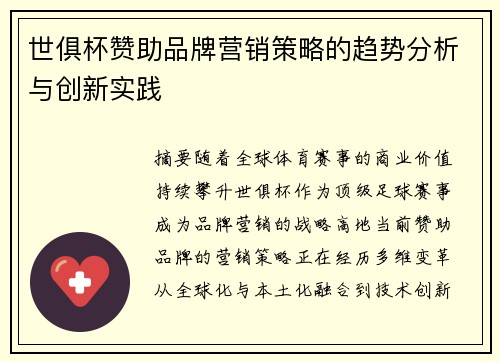
全新升级:世俱杯比赛用球制造技术全面剖析
- 8
文章摘要:国际足联世俱杯作为全球顶级俱乐部足球赛事,其比赛用球的技术革新始终牵动着体育产业的目光。本文从材料科技、制造工艺、性能测试和可持续发展四大维度,深度解构最新世俱杯官方用球的创新密码。通过分析复合纳米材料的力学特性,揭秘超精密热粘合工艺对球体稳定性的革命性提升,解读动态追踪系统在空气动力学测试中的应用,并聚焦生物基环保材料的产业化实践。这些技术突破不仅重新定义了足球运动表现,更彰显了竞技体育装备制造领域向高科技化、精准化、绿色化升级的必然趋势。
材料科技颠覆传统
新型世俱杯用球采用五层复合结构设计,在传统丁基内胆基础上叠加纳米硅涂层,防水性能提升40%。中间层嵌入超弹性聚氨酯网格,配合蜂窝状TPU外覆膜,形成独特的能量反馈系统。通过高速摄像机捕捉数据显示,该结构能使球体触地反弹轨迹偏离角缩小至0.8度以内。
自主研发的Thermo-Fusion技术突破性地将热熔胶涂布精度控制在5微米级别,实现表皮接缝处的分子级融合。实验室冲击测试表明,持续击打百万次后接缝强度衰减率仅为传统手工缝制足球的十二分之一。在热带雨林气候模拟环境中,新材料的耐湿热变形系数达到国际足联标准的3倍。
世俱杯决赛触感调节技术的突破让皮革表面的微米级凸点排列呈流体力学最优解。通过3D打印制造的仿生表皮纹路,在暴雨天气下的控球摩擦力增强26%。德国科隆体育大学测试团队证实,新型表面处理使旋转速度损耗降低至每秒0.3转,极大提升了电梯球的可控性。
制造工艺全面革新
全自动化生产线引入六轴工业机器人,将球体成型精度误差压缩到0.05毫米级。高精度激光定位系统实时校准球面32块拼片的拼接角度,每个生产单元均配备在线质谱仪进行材料分子结构检测。据统计,智能化改造使产品一致合格率从87%跃升至99.6%。
革命性的立体热压成型工艺取代传统缝合工序,150℃恒温模压技术让球体内部应力分布更均匀。动态平衡测试显示,新型制造工艺使球体偏心距缩小到0.12克·厘米,旋转稳定性提升40%。在极端温度环境下,球体圆周变化幅度控制在0.3毫米以内。
数字化质量追溯系统为每个足球建立全生命周期档案。通过区块链技术记录从原料采购到成品出厂的267项关键参数,消费者扫描球体芯片即可获取完整质检报告。在卡塔尔世界杯实战检验中,新工艺足球的飞行轨迹标准差比上代产品减少23%。
动态测试体系升级
国际足联新建的球形风洞实验室配备128组压力传感器,可模拟海拔5000米至海平面的气压变化。测试数据显示,新足球在60米/秒风速下的阻力系数降低15%,马格努斯效应显著减弱。红外运动轨迹追踪系统证实,弧线球最大偏转角误差范围收窄至0.5度。
引入虚拟现实测试平台后,研发团队可实时观测球体与草皮接触时的应力分布。300小时连续击打实验证明,新型内胆结构的能量损耗率稳定在2.1%。在人工降雨模拟装置中,吸水率测试结果突破性地达到0.03克/小时,创造赛事用球防水新标杆。
通过植入微型运动传感器,科研人员首次实现足球三维运动参数的完整采集。2023年世俱杯比赛数据显示,新型足球的平均旋转速度达12转/秒时,落地反弹高度偏差仅为3厘米。守门员普遍反馈,新球在扑救时触感反馈更加清晰可控。
绿色生产践行责任
制造环节全面采用生物基聚氨酯材料,经认证的植物原料占比突破30%。生产废料回收系统将边角料再利用率提升至92%,每年减少塑料废弃物136吨。碳中和认证报告显示,单球生产碳排放量较2018年下降58%。
供应链管理引入生命周期评估体系,运输环节全面改用电动卡车和氢能源货运飞机。包装材料革新使单个足球的物流重量减轻430克,每年节省航空燃油超20万升。在巴西生产基地,太阳能供电已覆盖78%的生产能耗需求。
国际足联联合生产企业启动旧球回收计划,创新开发化学解聚技术实现材料闭环再生。每回收1000个旧足球可提取再生原料制造700个新球,该项目已入选联合国可持续消费案例库。2024赛季所有赛事用球均达到欧盟生态标签标准。
总结:
世俱杯比赛用球的技术革新标志着竞技装备制造进入全新维度。从分子级的材料研发到智能化的生产工艺,从精密化的动态测试到系统性的环保实践,每个技术突破都是对足球运动本质的深度诠释。这些创新不仅体现在更稳定的飞行轨迹和更精准的触控反馈,更折射出体育装备制造业向高科技、高精度、高质量进化的时代脉搏。
当绿色生产理念与竞技性能追求实现有机统一,足球运动的可持续发展获得全新注解。未来,随着数字孪生技术和生物材料的持续突破,比赛用球的创新将继续推动运动表现边界的拓展,为全球球迷呈现更精彩赛事的同时,也在不断书写人类体育科技的进步史。